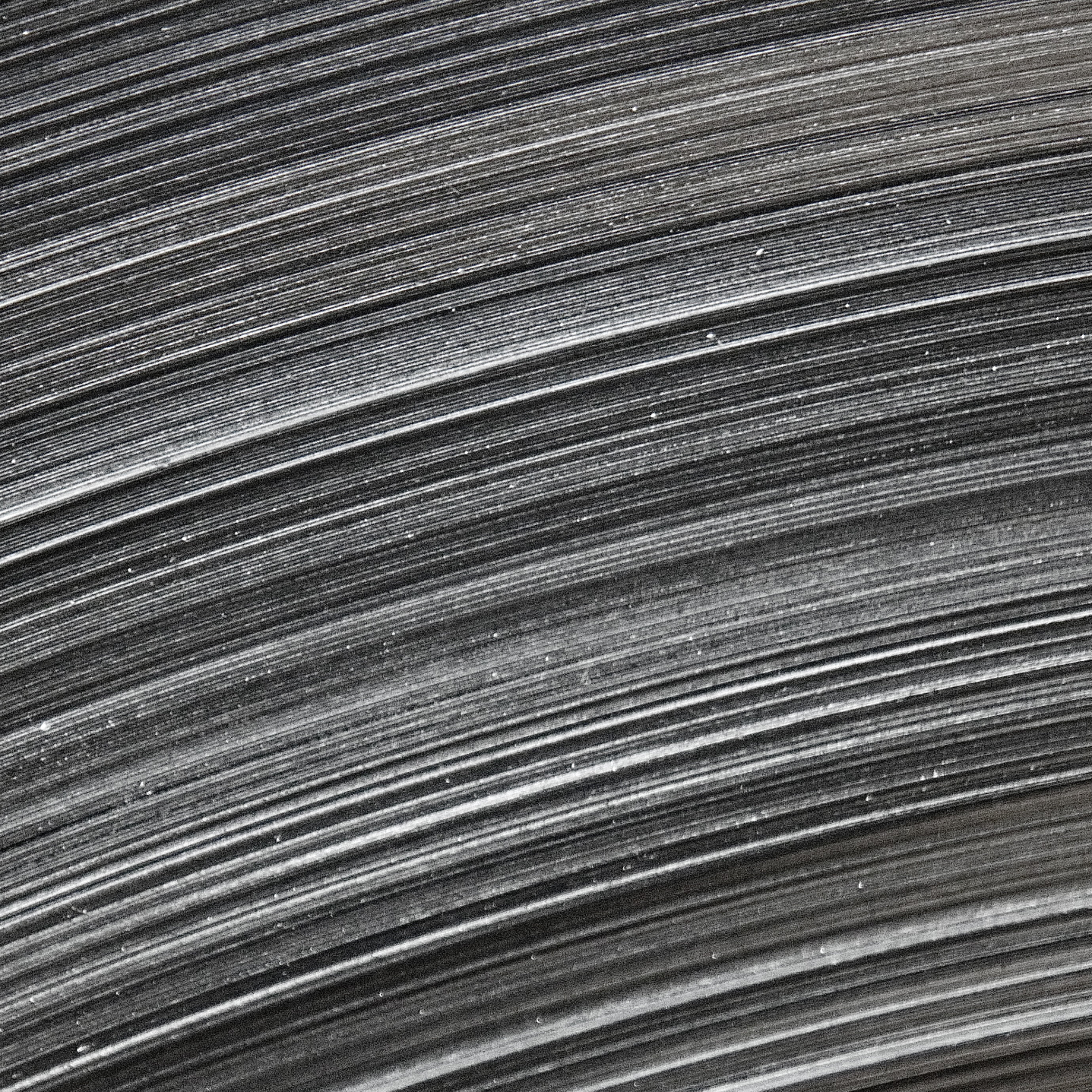
Tinned Copper Foil
Hot Dipped Tinned and Electroplated Tinned Copper
We supply high-quality Tinned Copper Foil in both Hot Dipped and Electroplated tinning. For corrosion resistance and conductivity, Tinned Copper is ideal for electrical, shielding, and industrial applications.
Thickness:
0.05mm-1mm for Copper Foil, strip and blanks. Other thicknesses available on request.
Width:
Standard width 305mm, larger widths are available on request, we can slit down to 3mm or less dependent on application.
Temper:
Soft (annealed), quarter hard, half hard and hard, full hard. We do have the ability to do other special tempers on request.
Tinned Copper Products that we Supply:
Tinned Copper Foil Uses:
Transformers
Screens
Shims
Architectural
Gaskets
Connectors
Marine
Automotive
Radiator Fins
To aid with preventing the tarnishing/oxidising of copper
Applications of Tinned Copper Foil
Electrical Wiring & Grounding – Used in cables, busbars, and grounding systems for reliable conductivity.
EMI/RFI Shielding – Reduces electromagnetic interference in sensitive electronic equipment.
Soldering Applications – Tin coating enhances solder-ability, making it ideal for circuit boards and electronic components.
Industrial & Marine Use – Resistant to oxidation and corrosion, making it perfect for harsh environments.
DIY & Craft Projects – Popular in custom electronics, stained glass, and decorative applications.
What Is Tinned Copper Foil?
Tinned copper foil is a thin sheet of copper coated with a layer of tin, combining the excellent conductivity of copper with enhanced corrosion resistance. This makes it a preferred choice for electrical, shielding, and industrial applications where durability and longevity are essential.
Hot-dipped tinned copper → is when copper has been coated with a layer of tin through a process known as hot-dip tinning. In this process, the metal is dipped into molten tin, which bonds to the surface, forming a protective coating.
This tin coating provides several benefits:
Corrosion Resistance: The tin layer protects the underlying metal from oxidation, rust, and other forms of corrosion, extending the metal's lifespan.
Enhanced Solderability: Tinned metal surfaces bond more easily with solder, which is beneficial in electrical and electronic applications where strong, conductive connections are needed.
Improved Conductivity: While tin itself isn’t a highly conductive material, it protects the metal from oxidation, ensuring that the conductive properties of the base metal (often copper) are preserved over time.
Electroplated tinned copper → is copper that has been coated with a thin layer of tin through an electroplating process. Unlike the hot-dip method, electroplating uses an electric current to bond the tin to the copper, creating a smooth, uniform, and relatively thin layer of tin on the copper surface. This tin coating enhances the properties of the copper in several ways:
Key Benefits of Electroplated Tinned Copper
Corrosion Resistance: The tin layer acts as a barrier against oxidation and corrosion, especially important in environments with moisture or salt exposure. This protection is particularly useful for copper, which can oxidise when exposed to air and moisture.
Improved Solderability: Electroplated tinned copper is highly solderable, making it ideal for electrical applications that require reliable and durable connections, such as wiring and electrical connectors.
Enhanced Conductivity: While tin itself is less conductive than copper, the tin coating helps preserve copper’s conductivity by preventing oxidation over time. This ensures the copper remains conductive and reliable in applications where stable electrical flow is critical.
Thin and Uniform Coating: The electroplating process produces a very even, thin layer of tin. This is beneficial for applications that require precision, as the layer does not add much thickness to the copper and maintains its flexibility.
More of Our Metal Products